Produktionslinje X-line 5 till Axelent
Produktionslinje för tillverkning av nätväggar
Vi har gjort ett djupdyk i ett av våra stora projekt tillsammans med Axelent som kommer stå helt färdigt under hösten 2023. Det handlar om en helt ny produktionslinje – X-line 5 som med ökad produktivitet, robusthet och smidig navigering tar Axelent in i nästa steg på deras utvecklingsresa för ännu fler säkra arbetsplatser över hela världen. Följ med på denna intervju med projektledare Sara Ekman från Axelent och Andreas Sandberg från Axelent Engineering.
Sara Ekman, projektledare Axelent
Berätta lite om denna produktionslinje och vad den producerar
– X-line 5 är en ny produktionslinje som tillverkar våra nätväggar i olika storlekar. Den kan tillverka en bredare produktflora än vad våra tidigare produktionslinjer gjort, med bättre prestanda och kvalitet.
Vill du berätta lite om din roll, och din delaktighet i det här projektet?
– Jag började på Axelent våren 2022 som projektledare och blev delaktig i det här projektet när maskinen redan var beställd. Min roll har genom processen varit att se till att produktionslinjen tillverkas i rätt takt, och att alla delar levereras i tid. Det har även varit min roll att följa upp hela förfarandet kring installationen och vara spindeln i nätet gentemot alla involverade leverantörer, vilket har inneburit en tät kontakt mellan personal hos oss och på Axelent Engineering. Mycket handlar ju om problemlösning under projektets gång så att det ska flyta på så smidigt som möjligt.
– För min del har det förstås handlat otroligt mycket om kontakten med underleverantörer – där Axelent Engineering är en stor del men även flera andra aktörer. Det rör allt från att se till att alla får rätt information om tidsplan, installationer, till vilka personer som ska vara på plats och när så att de olika aktörerna kan samverka.
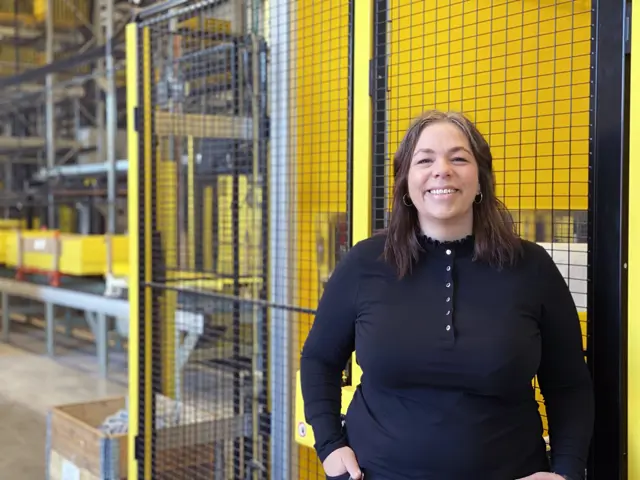
Vilka är de största utmaningarna skulle du säga med ett så stort projekt?
– Oförutsägbara händelser är alltid en utmaning, och dem kommer man alltid få räkna med. Det är många involverade och samverkan mellan alla olika aktörer är också förstås en utmaning som ställer krav på tydlighet och ständig kommunikation. I min roll som projektledare är det viktigt att få ihop helheten och se till att vi gör allt i rätt ordning och vid rätt tillfälle så att samverkan fungerar så bra som möjligt. Kommunikationen i ett så omfattande projekt är en nyckelfaktor.
Vad har varit mest givande under den här resan?
– Det som är mest utmanande är faktiskt också den biten som jag ser som mest givande – samarbetet med att jobba med så kompetenta och lösningsorienterade människor. Jag drivs av att se så mycket kompetens där vi kan mötas och diskutera, hela tiden med utgångspunkten att vi ska hitta en lösning. Det är högt i tak i samarbetet mellan oss på Axelent och Axelent Engineering. Jag upplever att åsikter tas emot på rätt sätt och man väljer att hela tiden söka lösningar på utmaningar. Det gör det enkelt att samarbeta.
Hur mycket kommer Axelent kunna öka sin produktionskapacitet genom den här produktionslinjen?
– Produktionen ökar vi stegvis med en helt ny produktionslinje men på sikt kommer detta självklart öka vår produktionskapacitet mycket. Genom alla uppdateringar och steg framåt som man gjort med denna produktionslinje gör sammantaget att den både kommer förenkla och effektivisera vår produktion.
Kan du berätta lite om hur samarbetet har varit med Axelent Engineering?
– Samarbetet har fungerat mycket bra! Vi har högt i tak, kan diskutera mycket och ha en tät och snabb kommunikation då det har behövts. Samarbetet mellan Axelent och Axelent Engineering har pågått under många år vilket gör att de känner oss väldigt väl. Det är förstås en stor fördel med deras förkunskaper när vi ska utveckla vår verksamhet.
Andreas Sandberg, projektledare Axelent Engineering
– Axelent och Axelent Engineering har jobbat länge tillsammans och har ett välutvecklat samarbete sedan tidigare projekt. I den här produktionslinjen behövdes en betydligt högre produktionskapacitet. För att nå de nya satta målen för det här projektet har vi både analyserat våra tidigare levererade produktionslinjer till Axelent, samt tittat på ny teknik och nya processer.
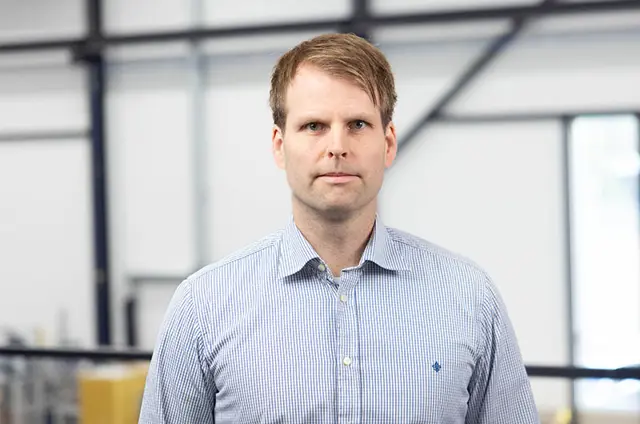
– Detta gör vi genom dels egna workshops liksom gemensamma workshops med teknikgrupper från båda företagen. Det är ett tight samarbete där alla verkligen kommer till tals med sina erfarenheter vilket ger en väldigt bra gruppdynamik. Det tekniska kunnandet och dom korta beslutsvägarna i gruppen ger förutsättningar för lyckade automationsprojekt.
– När vi pratar produktionskapacitet är samtliga nyckelfaktorer så som kvalitet, cykeltid, stabilitet, operatörsgränssnitt, serviceintervall mm lika viktiga få att nå en hållbar produktion över tid.
– Att arbeta med den senaste tekniken är en självklarhet för oss som befinner sig i en bransch där utvecklingen går väldigt fort framåt. Att konstruera, simulera och programmera maskinerna virtuellt innan dom fysiskt är uppbyggda ger möjlighet att verifiera processer tidigt i projekten och på så sätt korta projekttiden men även minska kostnaderna.
– Vi brinner för att göra våra kunder konkurrenskraftiga!
– Jag tycker att vi har ett fantastiskt samarbete som är helt öppet och prestigelöst där alla är med och bidrar med sina erfarenheter. Teknikintresset och drivet som finns i båda organisationerna borgar alltid för lyckade gemensamma projekt.
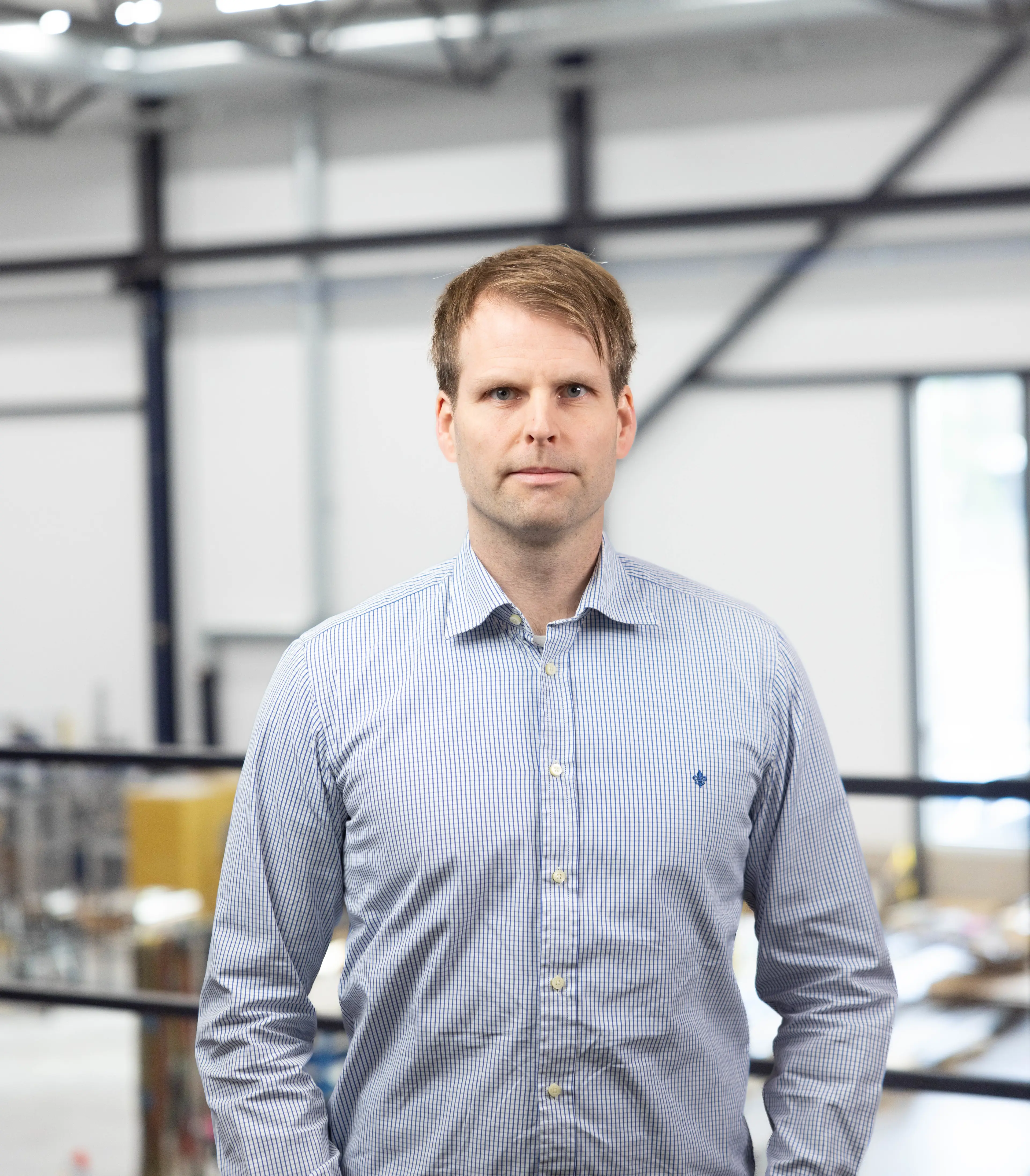
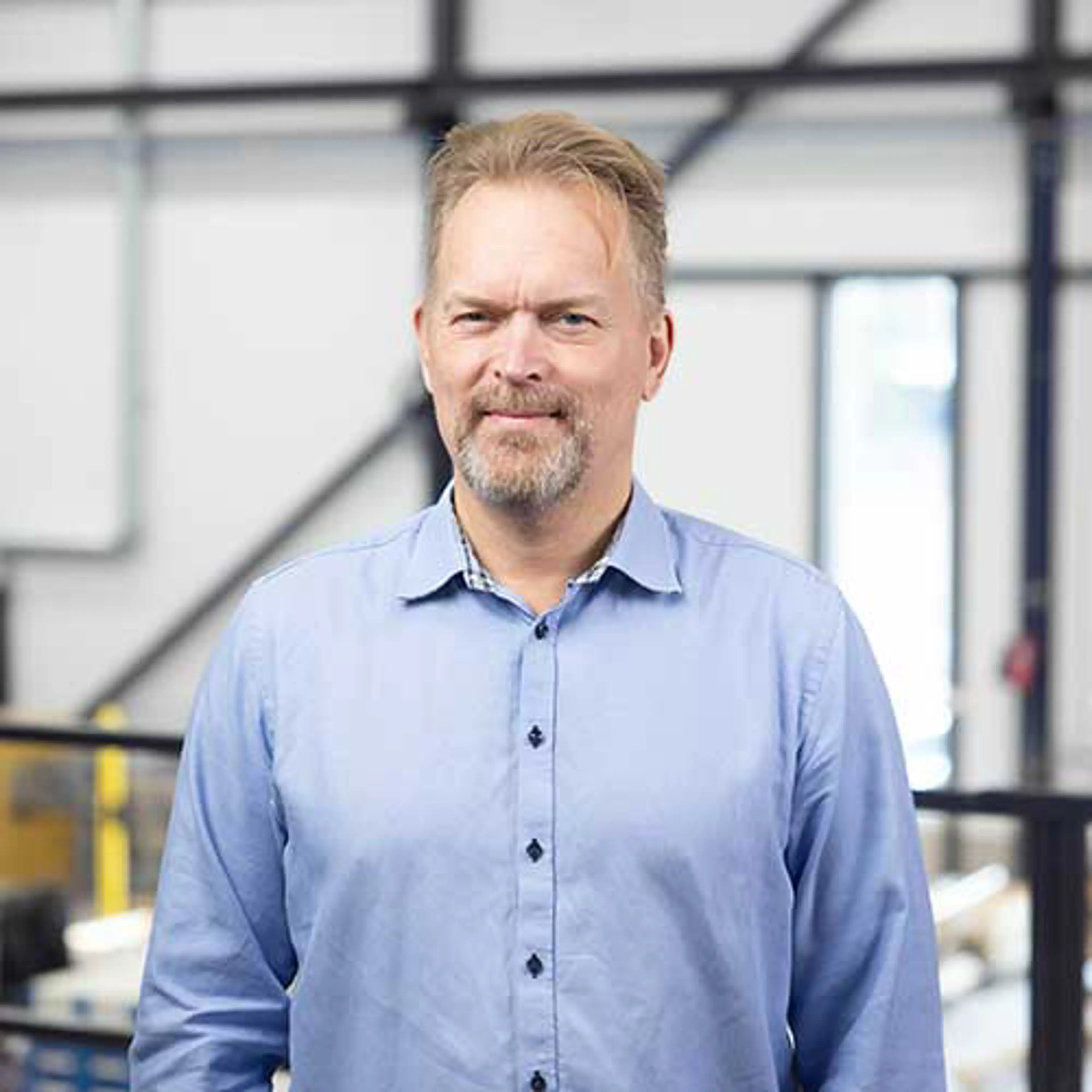
Frederik Sörensen